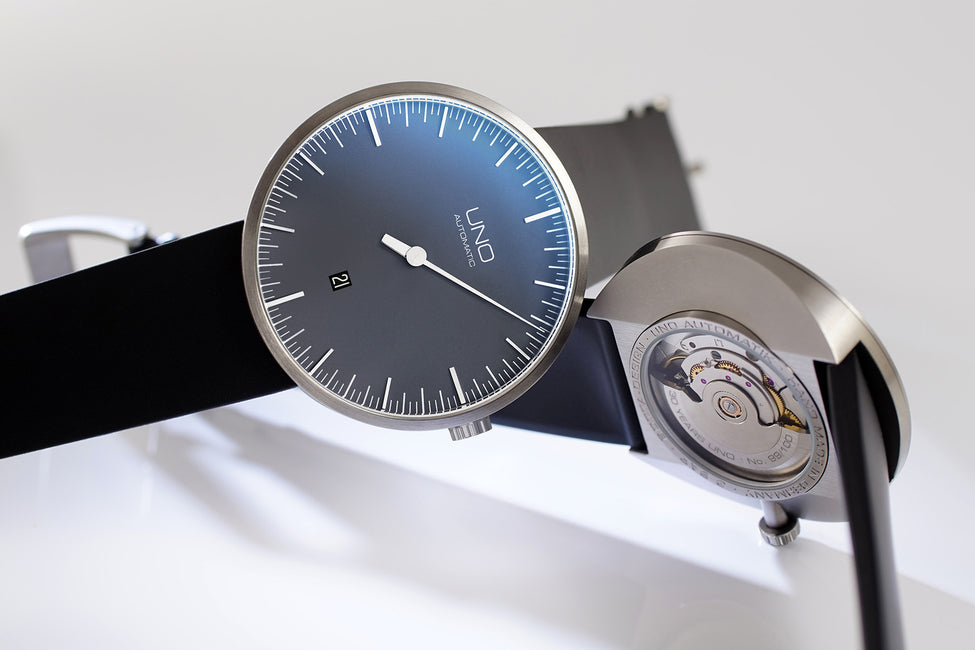
1. The development of design concepts
At BOTTA, every development always begins with a specific topic or task. The subsequent design process begins with the development of a content or design concept. At the end of this development there is a concrete watch model that reflects this topic or the solution to the task.
Example: The model UNO is based on the observation that wristwatches are becoming increasingly complex, confusing and arbitrary. The task we set ourselves at the time was: “What should a wristwatch look like that shows the time as simply and clearly as possible?”
Solution/Concept: The one-hand principle of the UN and that concept-specific dial.
2. Hand-drawn sketches as a basis for discussion
We usually start the design process with simple hand sketches that visualize initial ideas. We call these “thinking sketches.”
This is less about “painting impressive pictures” and more about developing concept ideas through drawings and presenting them in an uncomplicated manner.
The following video shows how drawings are created when a real drawing professional like our colleague Elschad gets started.
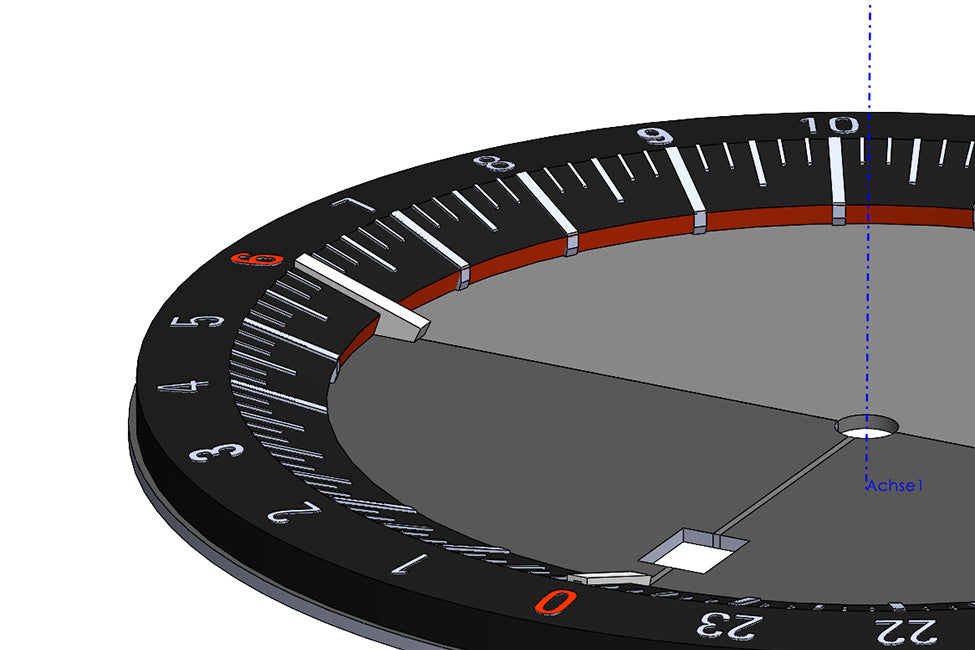
3. Realistic watch dial development on the computer
In the next step it becomes much more concrete: Here we build dials in proportion to the proportions on the computer. Initially in 2D format, later, if appropriate, also as a 3-CAD model. With precision in the hundredth of a millimeter range. This gives us a very realistic and meaningful impression. We can also change individual parameters such as line widths or colors very directly and in real time.
4. Variant creation in the CAD workflow
This process usually takes many months. Not least because of the creative breaks that are necessary to gain distance and optimize the concepts with a fresh perspective and, if necessary, develop further solutions. In the course of this process, dozens of different watch dial variants are created.
At the end of the process, the favorites are selected democratically by the entire office community.
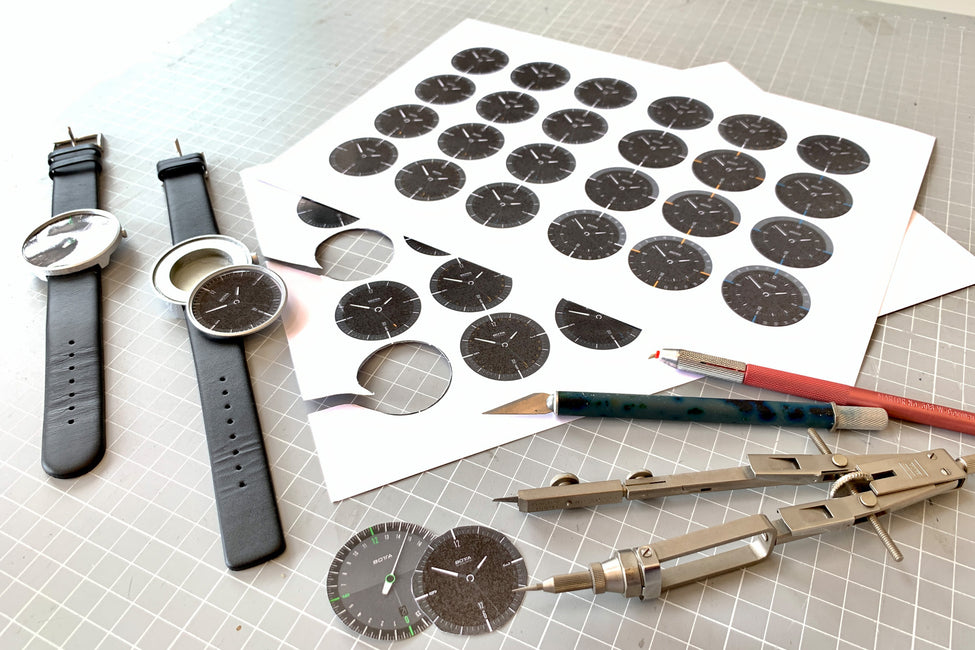
5. Photorealistic printouts for dial simulation
We create photorealistic prints of the three to five favorite dial designs on a special 2D printer, which can then be placed in a sample case together with the previously developed special hand. This is how we check the effect on the arm and the readability under real conditions. The favorite is initially produced as a sample and, if it passes the inspection, in series.
6. The design of specific watch cases
The development of a new case is even more complex than developing the watch dial. We start with hand drawings that outline the basic concept of the housing structure.
Here, too, we often draw several dozen basic ideas and details before we then construct selected candidates in CAD.
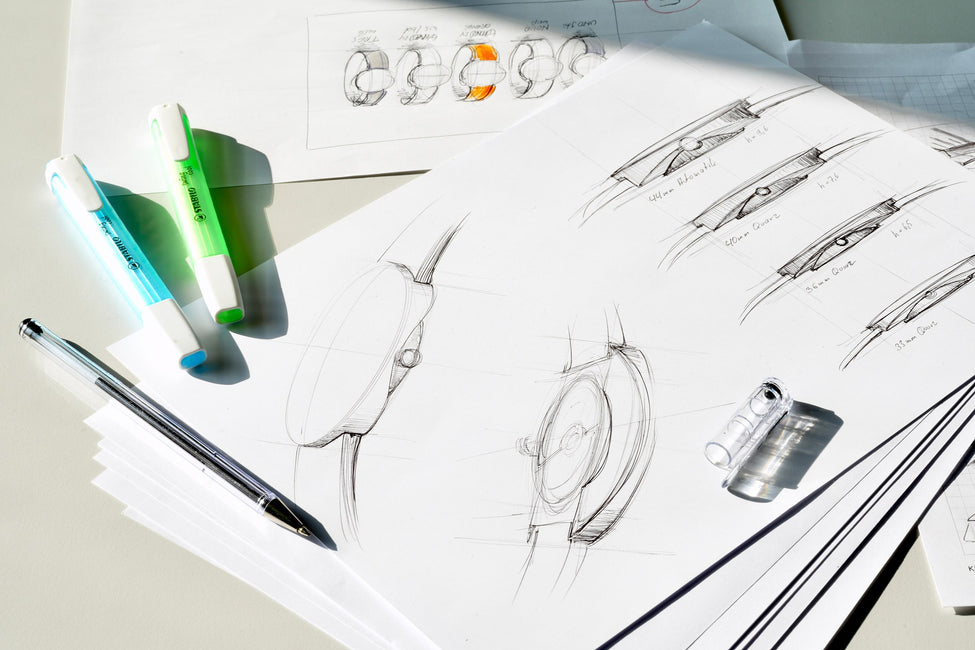
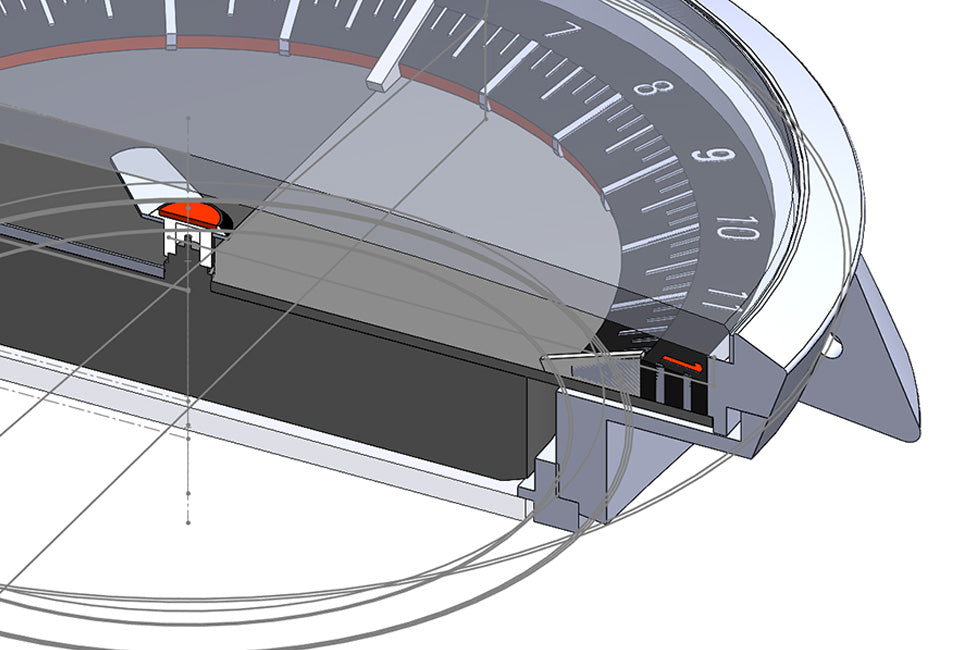
7. Enclosure design in the 3D Modeler
We always start the case design from the movement. This data is literally "decisive" for the basic geometry of the case. The movement diameter, movement height and setting stem height play a decisive role here.
The 3D design is parametric. This means that dimensions, wall thicknesses and geometries can be checked directly and changed interactively.
8. Pre-models in 3D filament printing
Another significant advantage of 3D design is the ability to print or mill models at a scale of 1:1 directly from the resulting data sets. For the first model series (proportional models) we use a high-precision filament printer. Using the patterns created in this way, the essential mechanical properties such as wearing comfort, dimensions and overall effect can be checked very effectively.
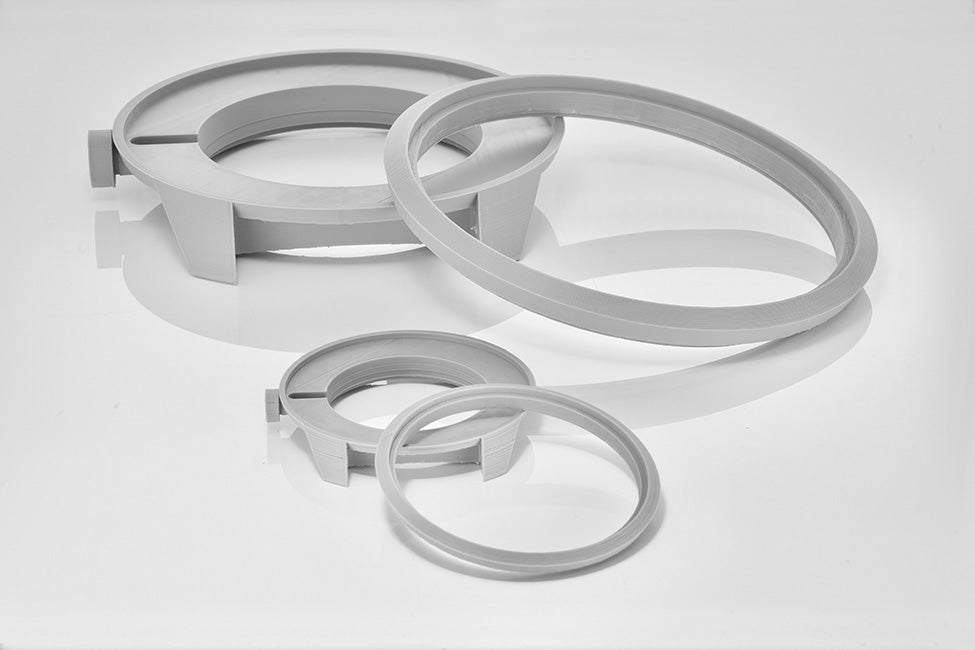
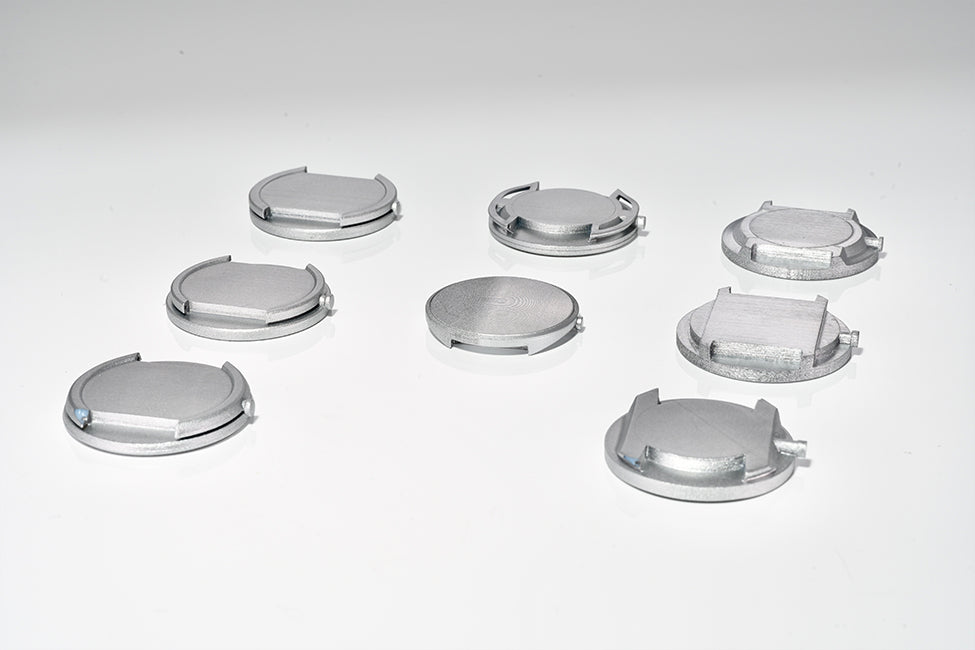
9. Housing models created stereolithographically
For an even more realistic assessment, we then have the favorites produced in a high-resolution 3D printing process. These parts are then finished and painted in our workshop. This results in enclosure models that are already visually very similar to a real metal enclosure.
10. Design models using the laser sintering process
From these 1:1 sample cases (using the stereolithography, laser sintering, or metal laser sintering process) we can then build complete sample watches without function, so-called design models, together with the other sample parts. These can then be created like normal watches and thus assessed realistically.
Here, just like in all previous sample stages, changes and optimizations occur which are brought to the most perfect possible result in so-called optimization loops (repetition of previous development steps). Visually and mechanically.
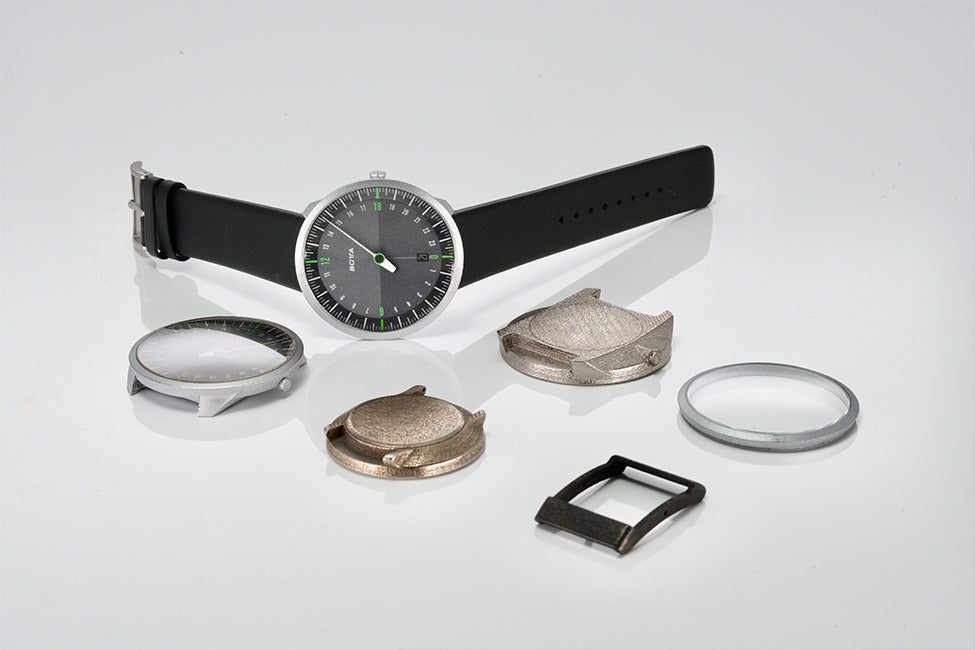
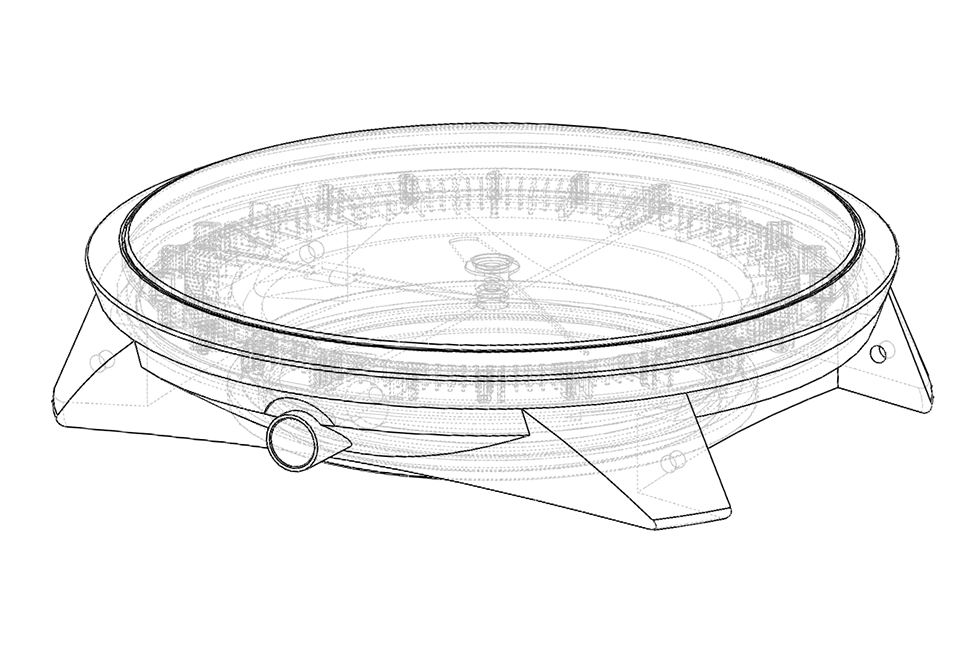
11. Data set creation for component manufacturers
After all optimizations have been completed, we fix the 3D data sets and send them to the respective producers. From there we receive corresponding countersigns for each component, which contain our dimensions but also the specific production conditions of the part manufacturer.
12. Prototype tests, tool making and pre-production samples
After our approval and an intermediate prototype phase, the manufacturer begins tool production. The first sample parts are produced with the finished tools. We use these sample parts to build pre-series models, which are then fully functional and allow a realistic wear test.
After passing the wear test (can take weeks or months), the series components are finally produced.
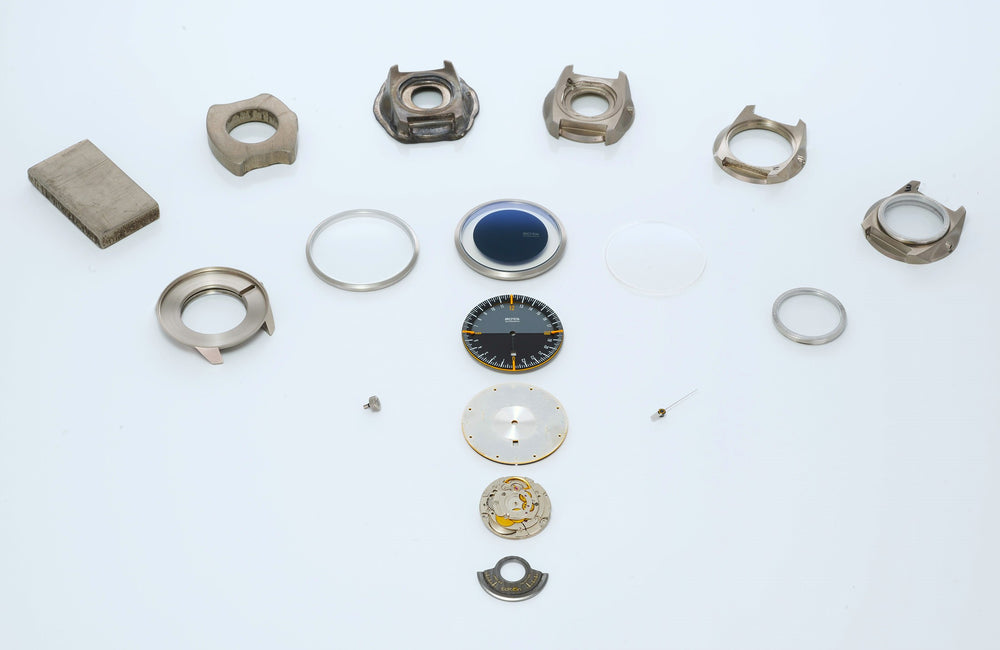
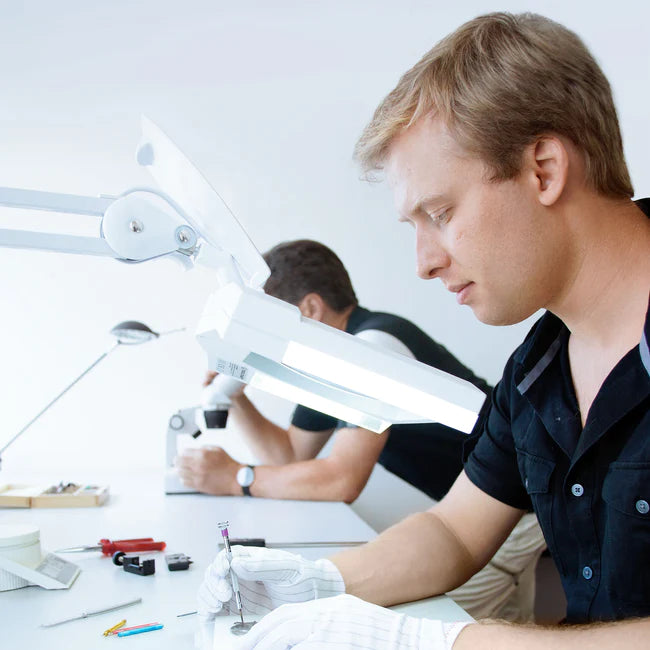
13. Inbound quality control
All series parts are subjected to a 100% incoming inspection (visual and technical) in our office in Königstein and are then sent to our watchmaker in the Black Forest appropriately preconfigured.
14. Assembly of the watches by the watchmaker
The watchmaker then carefully builds a complete watch from the individual components by hand. After assembly, the delicate time instruments are carefully readjusted by hand to ensure optimal operation. The watches are examined again using several test routines before they begin the journey back to Königstein.
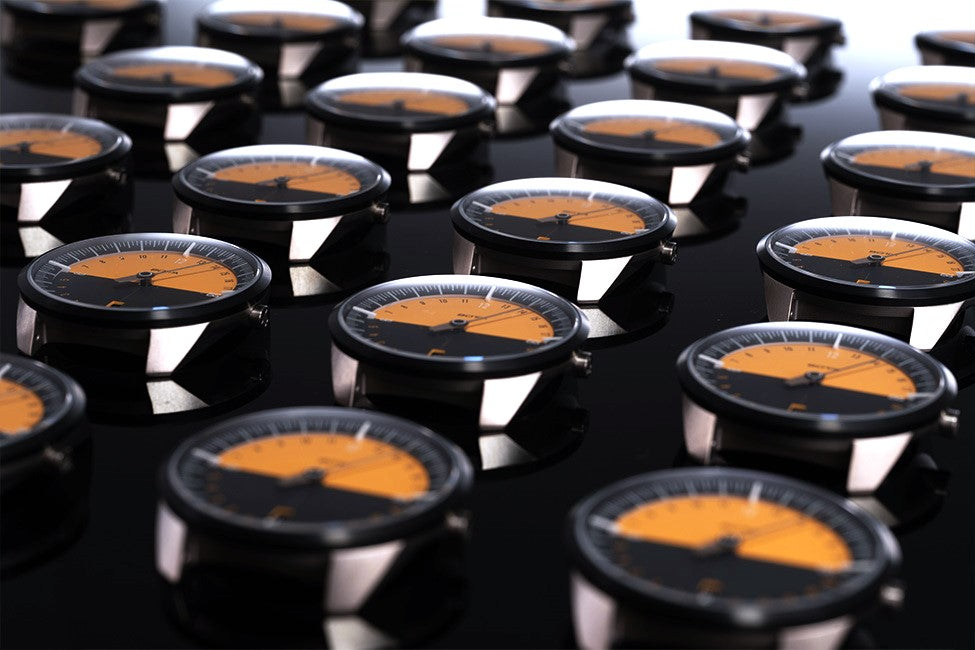
15. Quality control of the finished wristwatches
The finished watches are then subjected to another optical and technical incoming inspection and then sorted into our safes with the date of receipt. While in the safe, our quartz models simultaneously undergo an endurance test (function and accuracy).
16. Final inspection before delivery
After receiving your order, we will take the model in question out of the safe and check it again for technical functionality and optical quality. The desired watch strap is also assembled at this point.
For automatic watches, we also individually check the rate values and the respective power reserve. The values are documented in a test report.
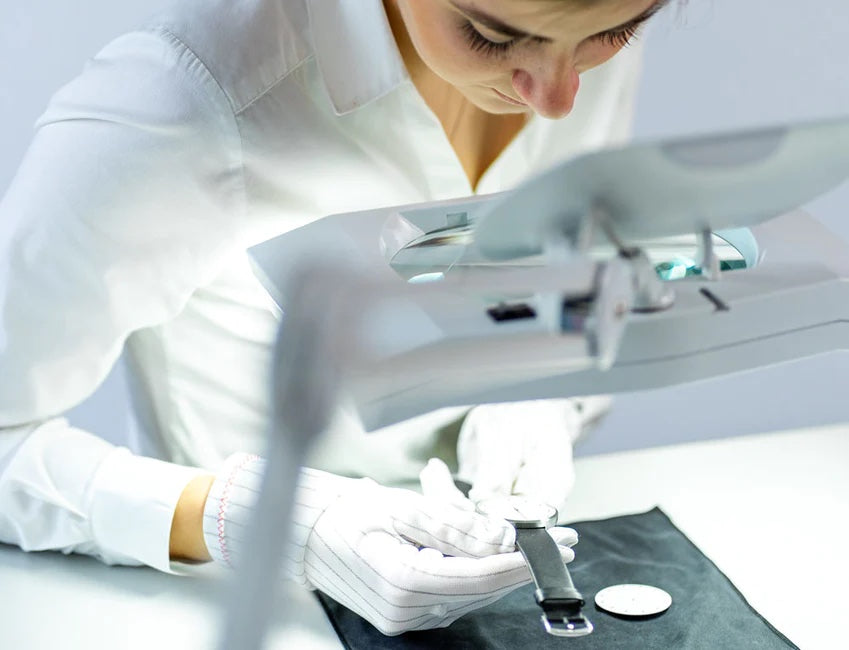
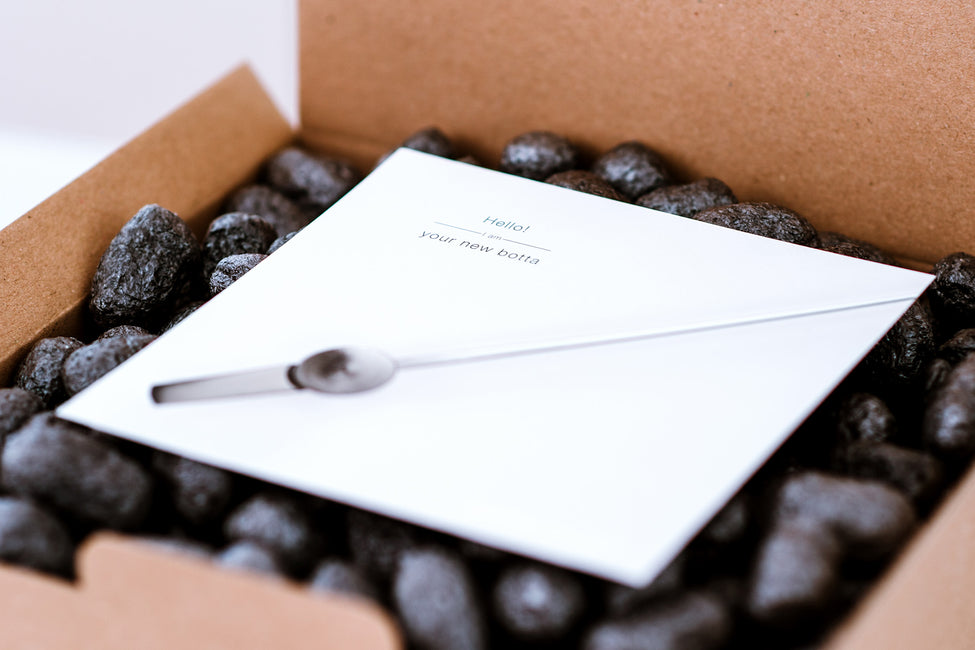
17. Packing and shipping
Finally, the watch is provided with the appropriate papers and documents and carefully packaged. As a rule, ordered quartz watches leave our office within the same or the following day. For automatic watches it takes a little longer due to the additional running tests lasting several days. After about 3-4 days they also travel to the customer.
18. The production of special series and small batches
Custom-made products, such as engravings or special requests, naturally require a longer processing time. In principle, there is almost nothing that we cannot produce. However, custom-made products require a certain minimum quantity.
Contact us, we will be happy to advise you on our options.
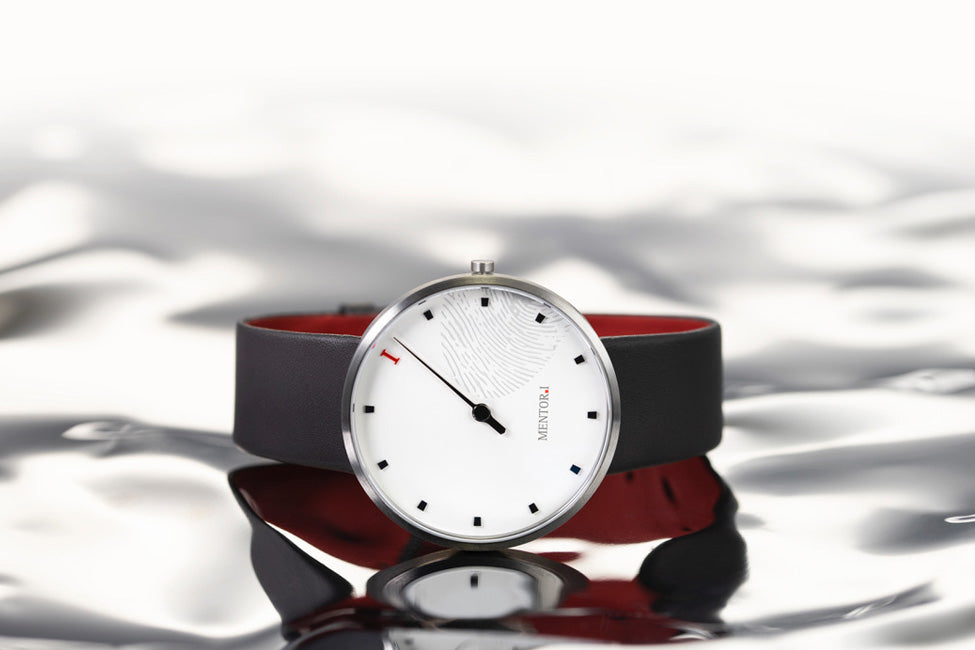
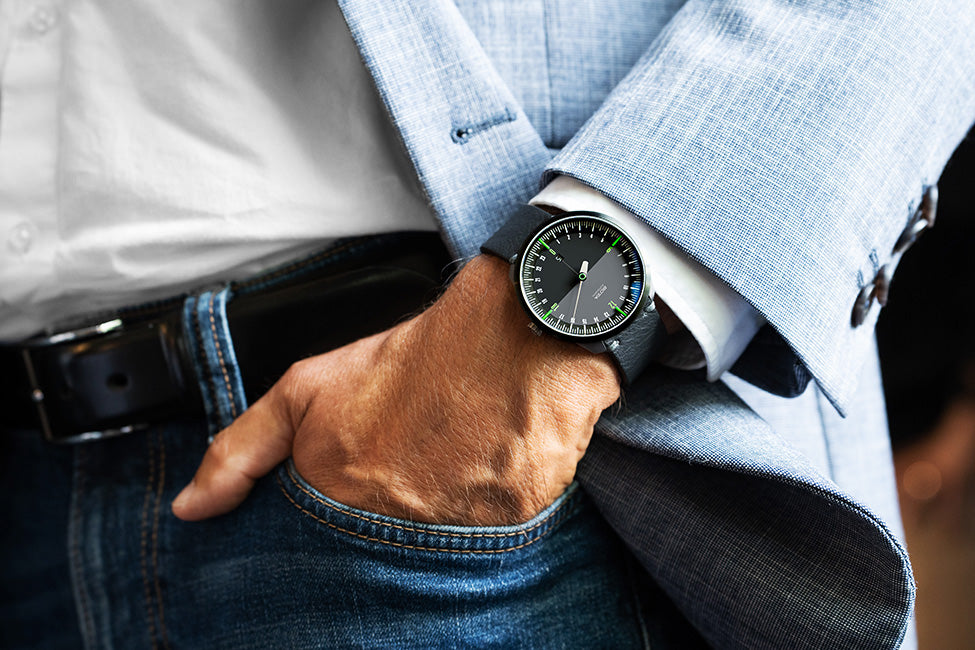
Résumé
Now you have a fairly detailed overview of how wristwatches are made at BOTTA. You'll probably be surprised at how many individual steps we take to create a finished watch.
Is this effort worth it, you may now be asking yourself. We say “definitely yes”. Just put one of our watches on and you will immediately feel the difference. Wear our watches for a certain amount of time, and you will notice that the way you deal with “YOUR TIME” changes positively. This is exactly why our work is worth it.